So, what can lithium-ion battery manufacturers, system developers, and operators do to reduce failures and ensure safety? There are three layers necessary for maintaining a safe and reliable battery system.
- Layer 1: Production Quality Control and Aging Tests
- Layer 2: The Battery Management System
- Layer 3: Put the Cloud to Work
These three layers are analogous to a rally, where we need a reliable car, a driver, and a co-pilot.
Layer 1: Production Quality Control and Aging Tests
The batteries can be seen as the rally car. For a rally, we need a reliable car of high quality.
However, cell manufacturers cannot guarantee 100% quality of every cell. Therefore, quality tests play a crucial role in traditional methods to prevent lithium battery failures.
End-of-line tests are done after production to see if a battery meets given quality standards. These tests are typically not very thorough, but they sort the obvious bad apples out of the lot. Shortly after production, analyses such as initial capacity or impedance measurements are often used to help identify faulty cells.
Certification tests are essential for every product as they must be fulfilled from a legal perspective. In these tests, standardized tests must be conducted, and the manufacturers must prove safety-relevant behavior.
To get an idea of the batteries’ aging behavior, both calendar and cycle tests are run over months and years in defined lab tests. However, these tests take time, are costly, only control a subset of batteries, and are not scalable for field-deployed systems. Batteries that are on our roads, in our homes, or connected to the grid experience way different environmental conditions and load profiles than can be tested in the lab.
Production quality tests evaluate only a specific point in time, which is why additional safety layers are needed.
Layer 2: The Battery Management System
The battery management systems (BMSs) can be seen as the rally drivers that focus on the road and continuously keep the car safe on track. However, they need more time and resources to see the bigger picture.
BMSs keep the batteries in their intended window of safe operation and minimize the impact of a single-cell failure on the affected pack or module. They do this by:
- Measuring the voltage, current, and temperature of the battery
- Calculating and monitoring the state of charge (SOC)
- Balancing cells to the same voltage levels for safe operation
If values come close to their edge values or exceed the boundary conditions, the BMS should bring the system to a safe state by changing operation or shutting the battery system. BMSs are a reactive, but necessary safety measure.
Unfortunately, there are shortcomings as BMSs:
- Only see the present condition
- Only see the cells within the corresponding battery pack
- Are limited in computing power and follow simple rules
Due to these limitations, BMSs cannot detect safety-relevant anomalies that happen within the specified value ranges, run deep analytics to calculate the battery state more accurately, or predict long-term trends. As prior incidents have shown, BMS limitations can play a role in lithium-ion battery failures, leaving companies at risk. This also increases the complexity of assessing safety risk because the quality of the BMS needs to be considered in addition to the manufacturing quality of the cells. Sensors can fail, leading to safety-critical events. Possible improvements can be made in sensor quality and computational power, leading to higher costs. But the question remains: If the BMS watches the battery – who watches the BMS?
Layer 3: Put the Cloud to Work
Cloud-based battery analytics can be seen as the co-pilots of the rally car, ensuring the correct route and strategy. While the BMS focuses on the immediate problems, the cloud oversees the bigger picture.
Cloud-based analytics add an additional safety layer to the BMS. The BMS data is gathered in the cloud, creating a historical database that enables deeper and more advanced analyses of the battery system's behavior as it operates and charges under real-world conditions. The analytics use physics-based battery models and machine learning to determine and predict battery aging and safety. Compared to the BMS, cloud analytics are a preventive safety measure as they can analyze long-term health trends and detect anomalies. This is very important as safety-critical aging mechanisms can even occur if the BMS keeps the battery within its intended value range for its entire life.
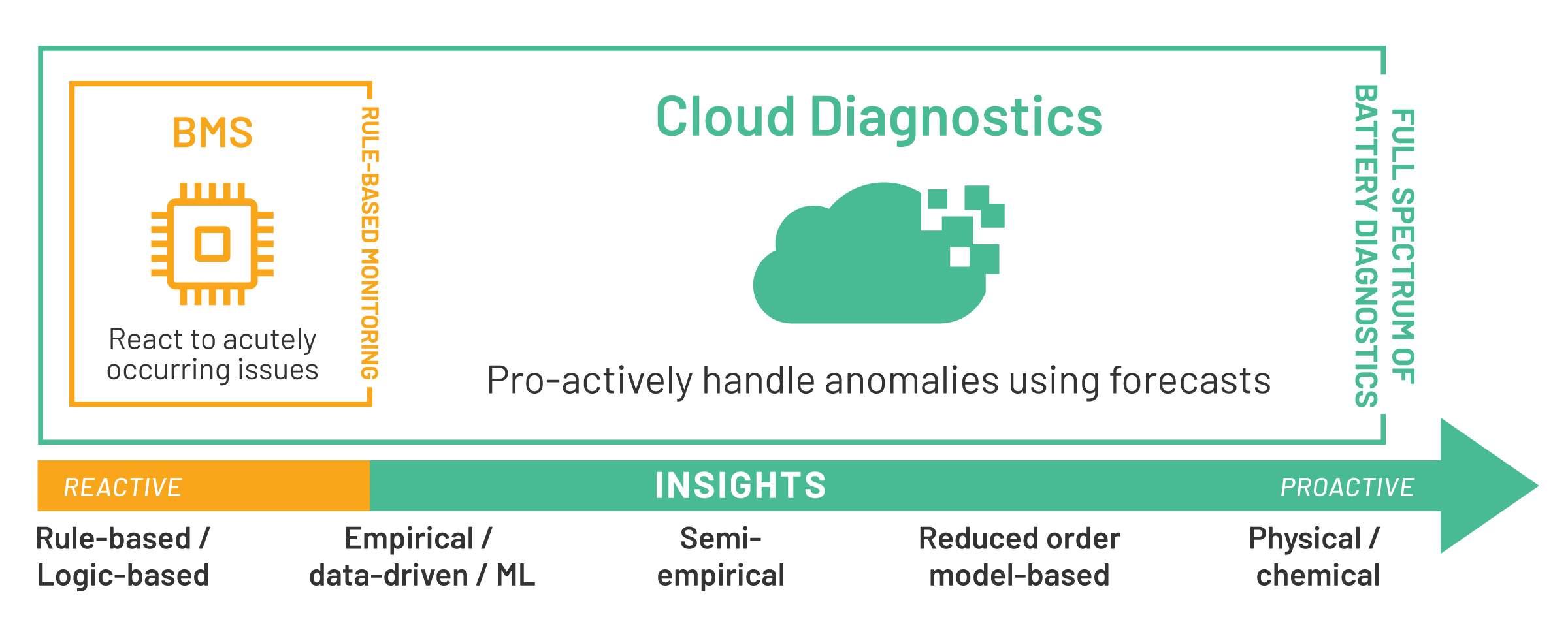
With the help of battery analytics software, owners and operators can:
- Track battery aging daily, during operation, and across all systems and suppliers
- Analyze battery behavior for multiple early-detection indicators
- Compare different systems and detect anomalies
- Enable preventative safety measures
- Accurately assess risk for every battery asset
Battery analytics software adds a vital safety layer to the BMS and production quality tests and delivers much-needed business intelligence to assess and mitigate risk across the battery lifecycle.
Three safety layers are needed for a reliable and safe operation, each covering different aspects. These include high production quality for initial safety, reliable battery management operation for short-term safety, and cloud analytics for long-term and strategic safety.
Want more information? Check out:
- The battery safety white paper by our CEO, Dr. Kai-Philipp Kairies
- Open circuit voltage analysis presented by our CTO, Dr. Georg Angenendt
- Many more blogs on battery analytics