"While everyone in the industry agrees that battery safety should be the top priority, the reality is that the expectations and pressures relating to growth create conflicting priorities, in addition to the pressures to commercialize new, innovative technologies. Higher energy densities, for example, inevitably mean more energy that can fuel the fire during a failure."
The focus on ever-increasing battery energy densities and cost reductions, combined with a dizzyingly fast ramp-up of global production capacities has brought LIB into countless applications. As more industry players enter the market and deploy at a rapid pace, safety incidents also increase. Battery fires and explosions have become a regular sight in the news and on social media.
Three events that caught worldwide attention:
- In 2019, a cell failure in a battery system at an APS facility in McMicken, Arizona, led to a thermal runaway and ultimately caused an explosion that injured several first responders.
- Between April 2021 and May 2022, over 80 electric buses and 4 bus depots burned down across France, Germany, and the UK.
- Since 2020 thousands of electric scooters have caught fire around the world – some in private homes, some in warehouses.
So, what are our options to prevent critical failures and make batteries—and clean energy—as safe as possible?
Apart from rigorous quality standards during manufacturing and passive battery management systems, cloud-based diagnostics have proven effective to prevent critical failures. The diagnostics, also known as advanced battery intelligence leverage existing field data streams and can be applied to any Lithium battery system without the need for any product modification. The concept of cloud-based analytics:
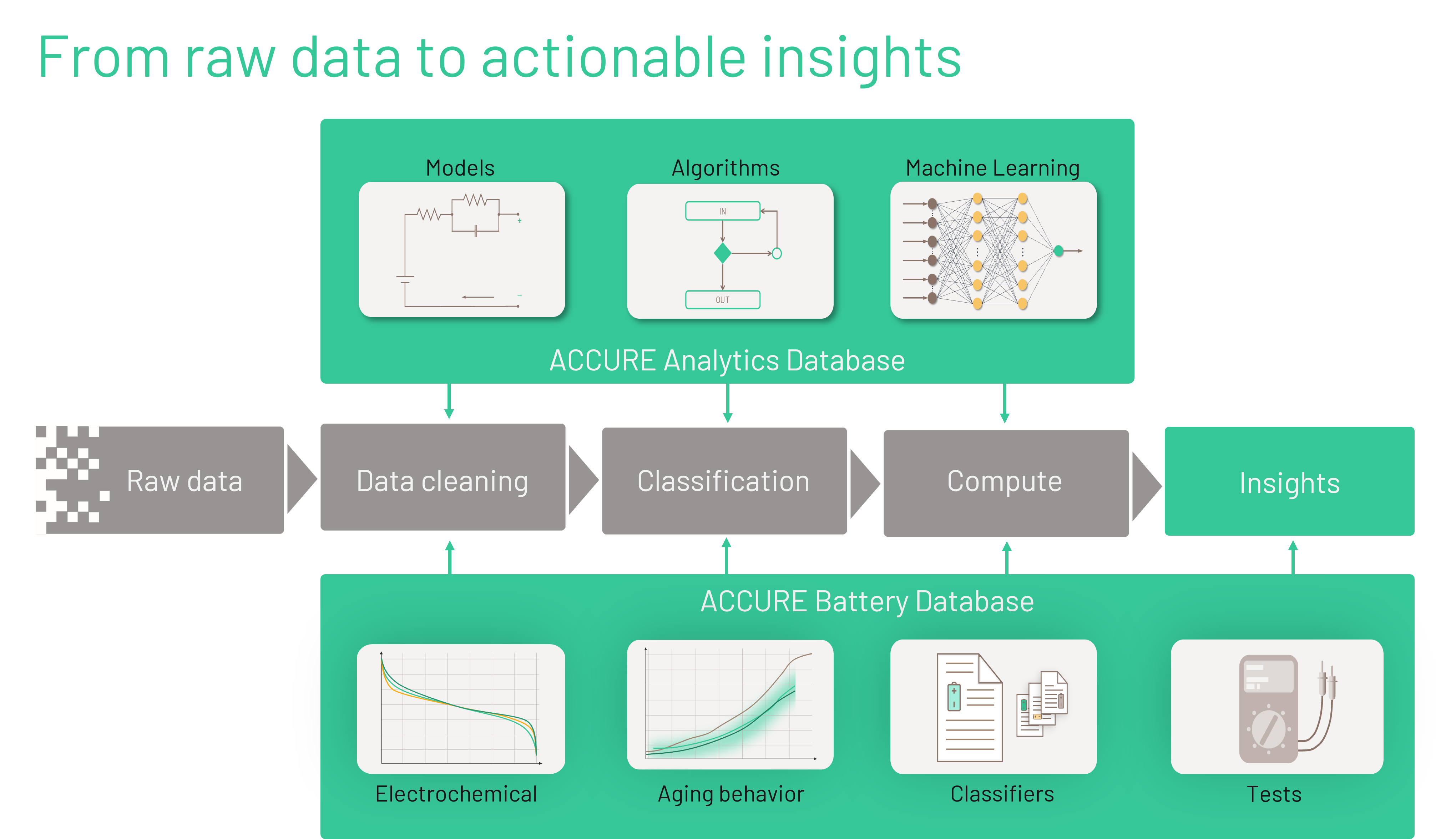
Step 1: Data acquisition
The continuous stream of measurements from the battery management systems (BMS) is passed to the communication bus and then pushed to the cloud where it can be stored, consolidated, and analyzed.
Step 2: Data pre-processing
To leverage the BMS data, extensive cleaning needs to be performed: outliers and systematic measurement errors in the raw data need to be detected and flagged as such. Every battery management system has its own (systematic and statistical) errors and idiosyncrasies that need to be understood to make sense of the data.
Step 3: Fault detection
Fault detection algorithms scrutinize the battery data to check for potential faults via changes in primary parameters such as voltage, temperature, and current or in secondary parameters such as impedance, a shift in the open circuit voltage curve, or the amount of active lithium in each cell. Tracking secondary parameters is also essential. Model-based algorithms that look for patterns across millions of similar cells, in operation, enables these safety algorithms to find anomalies before they become dangerous.
Step 4: Reporting
If a battery is identified as dangerous by the cloud analytics, automated warning notifications are generated to allow the operator to act – by bringing the system into a safe state and arranging for maintenance or replacement.
Keep reading on the Energy-Storage.News website.
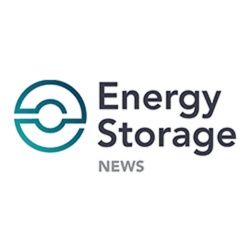