One-third of electric vehicle fires occur during charging and another third while parking.1 Although there still is a debate, errors in battery production or in the battery management system (BMS) have been addressed. The functioning of the BMS is usually limited to tracking the cells in the respective battery and does not have access to historical data or data from other battery systems. Consequently, the detection of anomalies or long-term analyses is very difficult or even impossible. Through online monitoring solutions, using predictive diagnostics by incorporating historical battery data, critical battery cell conditions can be detected at an early stage, and safety measures can be initiated before damage occurs.
Common Battery Fire Safety Measures
Despite the online monitoring solutions described, the risk of a battery fire cannot be excluded, which is why safety measures using fire protection materials in the battery system play a major role. Safety measures can be applied at the battery cell, battery module and/or battery pack level.
Currently, two main strategies are being pursued:
- Fire Resistant Coating: The battery housing is equipped with an appropriate fire protection coating so that the environment, and thus also the passengers, are protected from burning cells in the battery system. Accordingly, this measure is to be classified at the battery pack level.
- Thermal Propagation Prevention: By preventing thermal propagation through the use of safety-relevant materials between and/or on the cells, the fire in the battery is kept as small as possible so that there is little to no impact on the surroundings and thus the passengers. Depending on the battery design, this measure can be used at both the battery module and battery pack levels.
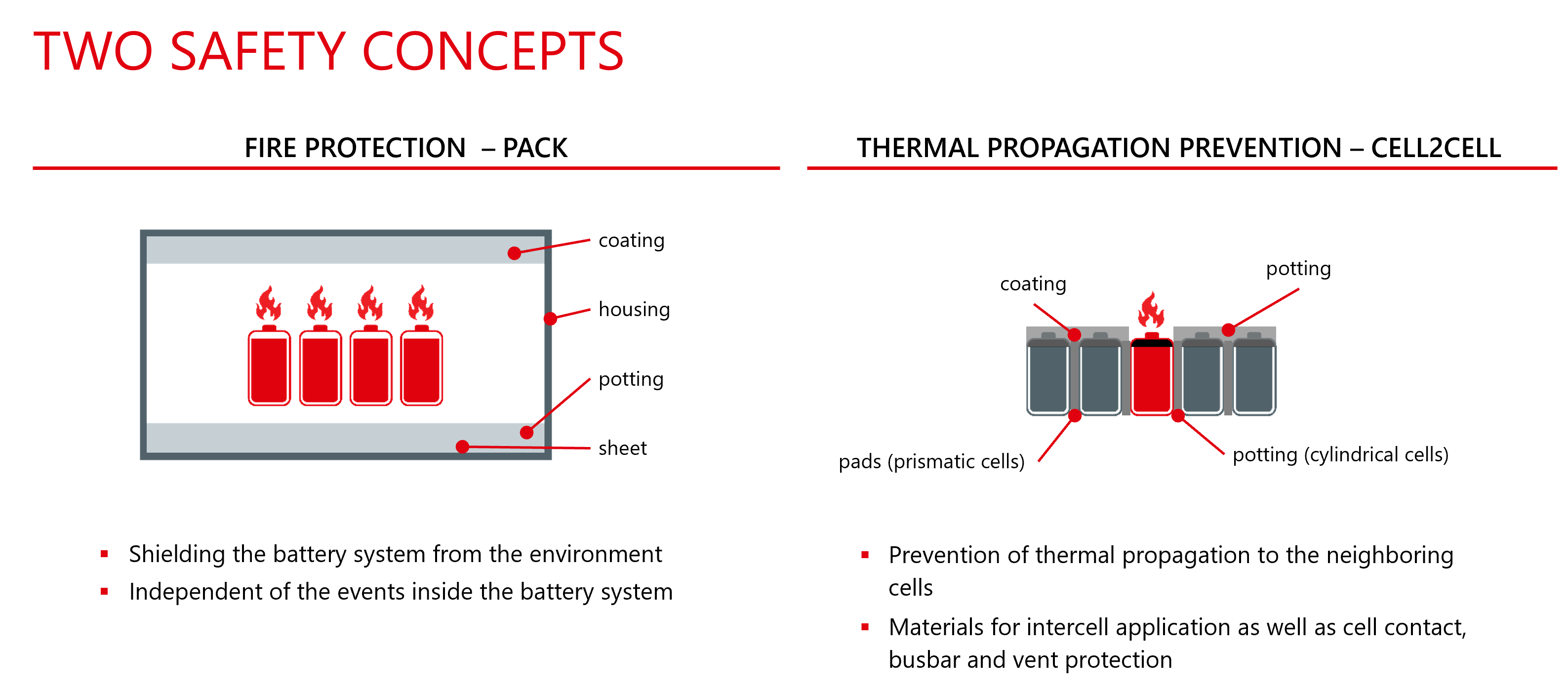
Fire Protection Materials for Battery Casing
Classic fire protection materials on the battery casing, often used on the inside of the battery lid, are composite materials that are currently found to be mica sheets. However, due to a more efficient production process and the demand for sustainable materials, the trend is towards liquid-applied fire protection coatings. The advantage of liquid-applied materials is that there are no pre-processes, such as pre-molding or cutting of the sheets, and the possibility of a fully automated and highly flexible coating.
Liquid-Applied Coatings for Battery Fire Protection
One possibility for an application process of a liquid material is the flat-streaming process,which is suitable for coating almost 2-dimensional components like the battery lid. The second coating method is spray coating, especially for 3-dimensional components like the battery housing. For liquid-applied fire protection coatings, different material classes are on the market, but mainly can be divided into organic material, for example epoxy, or aqueous inorganic systems.
The fire protection coatings can have intumescent properties, so-called heat foaming. This reaction creates a heat shield by separating the temperature source from the surface that should be protected. An important criterion is the carefully designed reaction control, in order, not only to avoid blocking venting channels, but also to prevent short circuits by creating contacts between components. The advantage of this material is the low initial coating thickness. An example of this class of material is Loctite EA 9400 from Henkel. For the Loctite EA 9400, there is an additional advantage: the application process via a flat streaming method, in which masking is not necessary due to the high coating accuracy. Also, due to the coating method, no aerosols are formed, which in turn means less effort regarding the production environment.
Another advantage is the lower material waste due to the controlled and precise process, which in turn allows a high sustainable use of the materials. Alternatively, the fire protection coating can also provide heat protection via a thicker initial coating thickness, whereby the material then has no intumescent properties. The advantage here is that no chemical reaction takes place in the battery during the thermal discharge event, and thus greater controllability can be ensured. An example of this is Loctite FPC 5060 from Henkel. As Loctite FPC5060 is a water-based inorganic system, no flames or smoke are generated by this material during the thermal runaway of battery cells.
Intercell Materials for Battery Fire Protection
Prevention of thermal propagation can also be achieved by intercell materials. This can be applied between the battery cells. The material class and property are decided by the cell form factors and the related stacking design. For cylindrical cells, potting materials or foams are often selected; for prismatic and pouch cells, sheet / pad type materials can be the best solutions.
Developments in Fire Protection Materials
Depending on the battery design, the material requirements vary. In principle, regarding fire protection, all materials must have low thermal conductivities and the high thermal stabilities as well as sufficient dielectric strengths. In addition to the fire protection requirements, specific properties are also needed regarding the mechanical behavior. More specifically, different levels of mechanical properties are required for the structural integrity of each design, such as elasticity, stiffness, yield strength, etc. Henkel offers bespoke pad solutions for individual customers by tailoring mechanical, thermal, and electrical properties for a variety of cell & system designs.
Today's electric-vehicle-dedicated platforms are new additions to the market. Therefore, safety-focused designs are not yet complete, nor are the material solutions. Innovative efforts to find the best fire protection for future battery systems are ongoing. Two opposing trends can be identified for future battery systems:
- Cell chemistries that offer greater safety due to lower fire capabilities are sought after (e.g. all solid state).
- Battery cells are becoming larger and larger, with correspondingly more capacity per cell and a larger impact in the event of thermal runaway.
Since the majority of battery systems will be based on the current lithium-ion batteries with liquid electrolytes in the next 10+ years, growing demands on safety-relevant materials can be observed. In particular, stability against hot particles over several minutes demands advanced material developments with outstanding properties.
Testing Battery Fire Protection
In order to be able to develop advanced materials quickly and close to the application, the required material properties must be predicted via simulations and the developed materials must be characterized via application-specific and standardized test methods.
Therefore, as a material development company in the field of battery materials, Henkel has built up a team of experts from the industry for the simulation of different battery scenarios. In particular, the simulation of the thermal runaway of battery cells with different designs and their propagation by understanding the heat propagation in the battery system, taking into account all material combinations used, plays an important role in the development of fire protection materials. Among other things, required thermal conductivities, specific heat capacities and mechanical properties can be derived from this.
An application-oriented test procedure was developed for the subsequent material characterization.
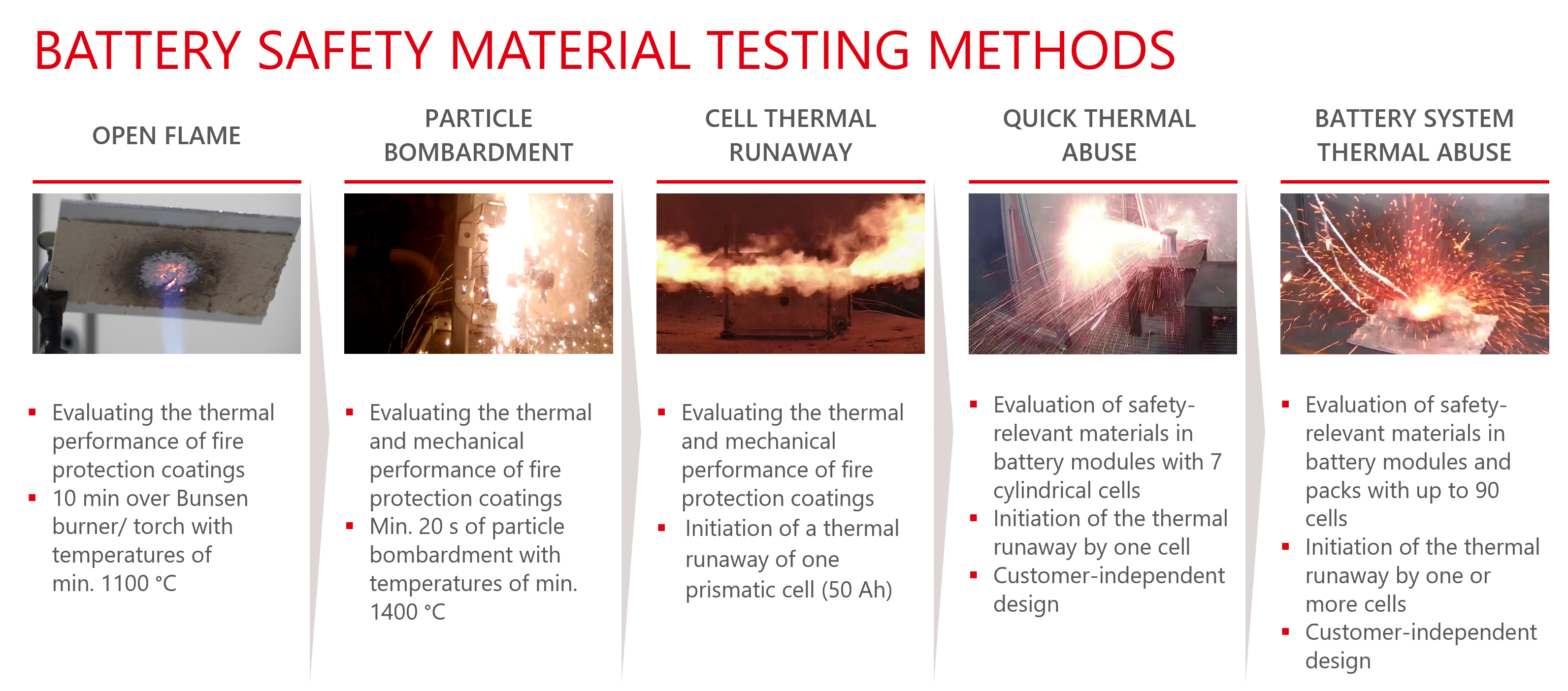
Open Flame Test
The test procedure is started with the in-house Open Flame Test, in which the heat shielding of the fire protection coating is determined by placing the sample above a Bunsen burner. Afterwards, the material is tested at test institutes for thermal and mechanical performance during a thermal runaway scenario.
Volcano Test
In the Volcano Test, the thermal propagation of a battery cell is simulated by a bombardment with, for example, burning aluminum particles. The delay or prevention of a shot through the coated battery housing material is evaluated.
Cell Thermal Runaway Test
If the fire protection coating meets the requirements, the next step of the test procedure, Cell Thermal Runaway, can be continued, in which the protective function of the fire protection coating during a thermal runaway is checked with a real battery cell, e.g. a prismatic cell with 50 Ah capacity.
Quick Thermal Abuse Test
In the QuickThermal Abuse methodology, either only the intercell materials, i.e. potting materials or foams, or the combination with the fire protection coating can be examined in the thermal propagation scenario in the so-called quick thermal runaway tests. In this test, 7 cylindrical cells are used in the simplest possible set-up, in which a cylindrical cell is triggered into a thermal runaway. This set-up is used for regular evaluation of new material developments as well as for validation of the simulations.
Battery System Thermal Abuse Test
In the final customer-unspecific test at the battery system level, the influences of several functional materials (thermal gap filler, thermally conductive adhesive, potting, foam, fire protection coating, sealing & gasketing) can be tested with over 90 battery cells in thermal runaway.
In conclusion, it can be said that the demands in the field of material development are constantly growing. This is driven by the need to conduct tests closely aligned with real-world applications and simulate material behaviors within those applications. The material requirements are becoming higher and more dynamic, particularly in the context of advancing battery designs to ensure both safety and performance.
Learn more about Electric Vehicle Battery Safety with Henkel Adhesives
1 Dr James Edmondson and Dr Richard Collins: Fire Protection Materials for Electric Vehicle Batteries 2023-2033, IDTechEx, Date retrieved: 1 August 2023 [https://www.idtechex.com/en/research-report/fire-protection-materials-for-electric-vehicle-batteries-2023-2033/897]